Reamers
Reamers are rotary cutting tools used for enlarging and contouring the interior walls of a pre-existing hole and can be used in a lathe machine, milling machine, or a drill press.
These high-speed steel reamers come with a breakdown of different shank types, sizes, diameters, and flutes.
Die Maker
Reamers
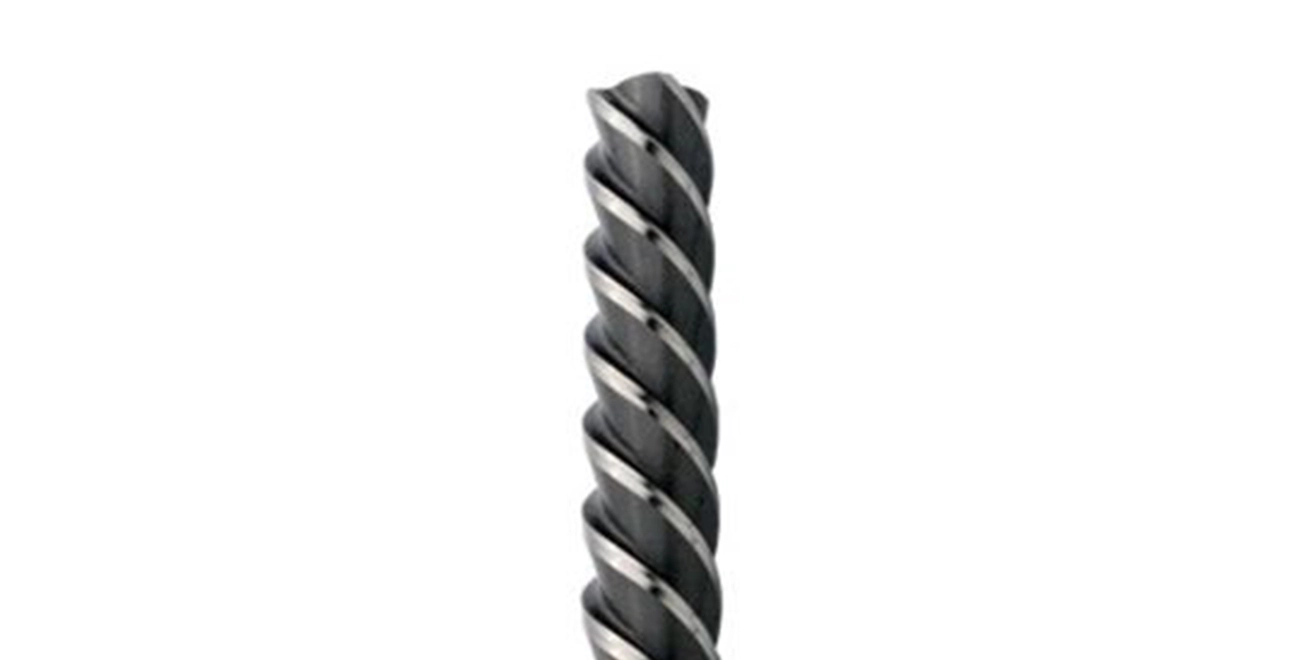
Die Maker Reamers are used to create tools such as die sets, punches, and steel rule dies.
Brown & Sharpe
Reamers
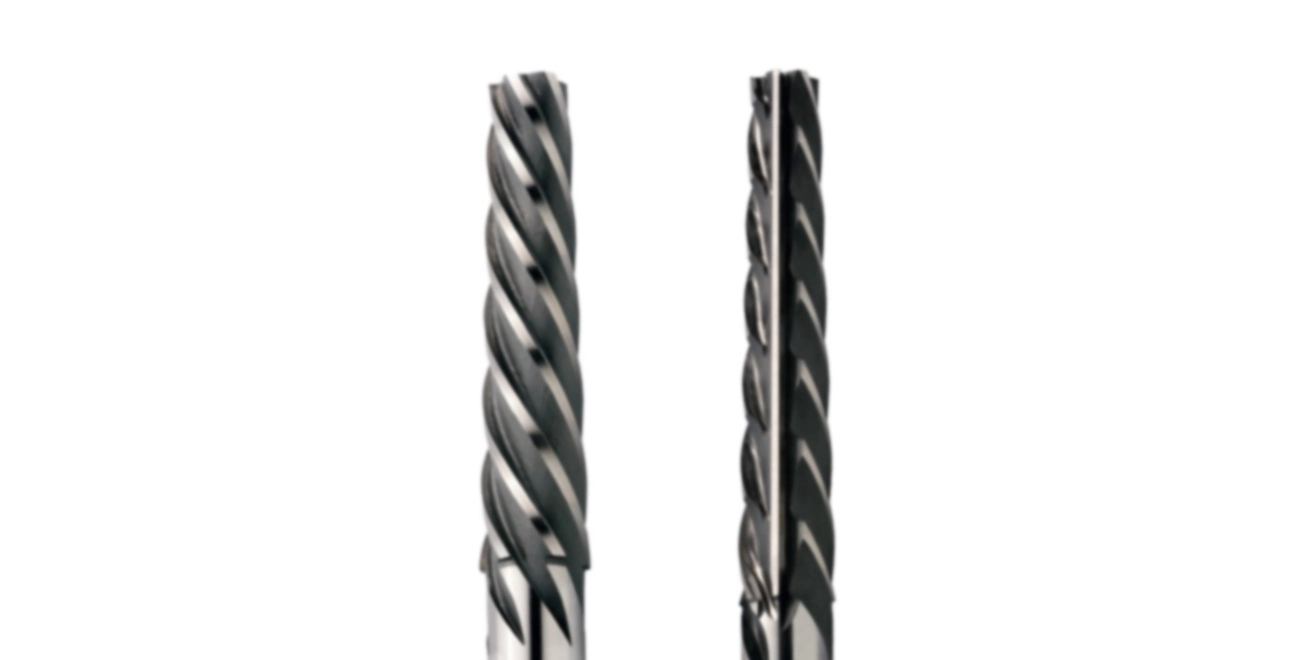
Brown and Sharpe Reamers, or Aircraft Taper Reamers, are used to finish B&S taper sleeves.
Jarno
Reamers
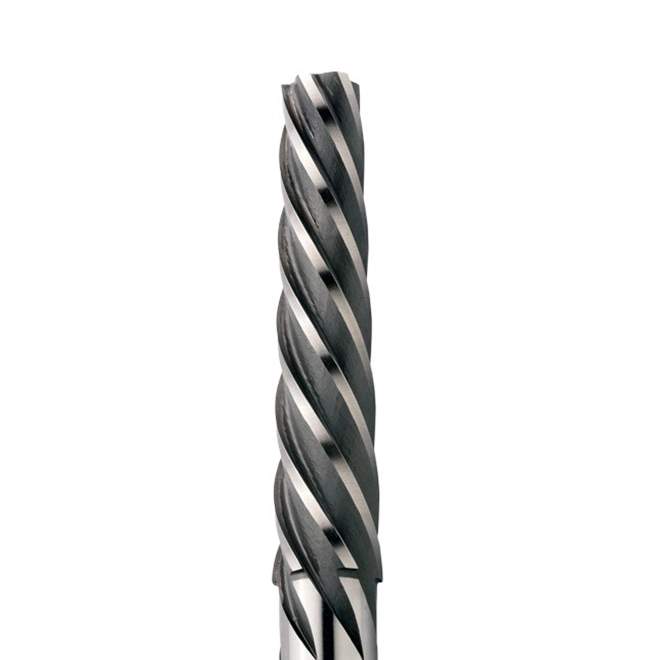
Jarno Reamers are used to finish jarno taper sleeves to hold cutting tools or holders in the spindles of machines.
Industry Specific
Reamers
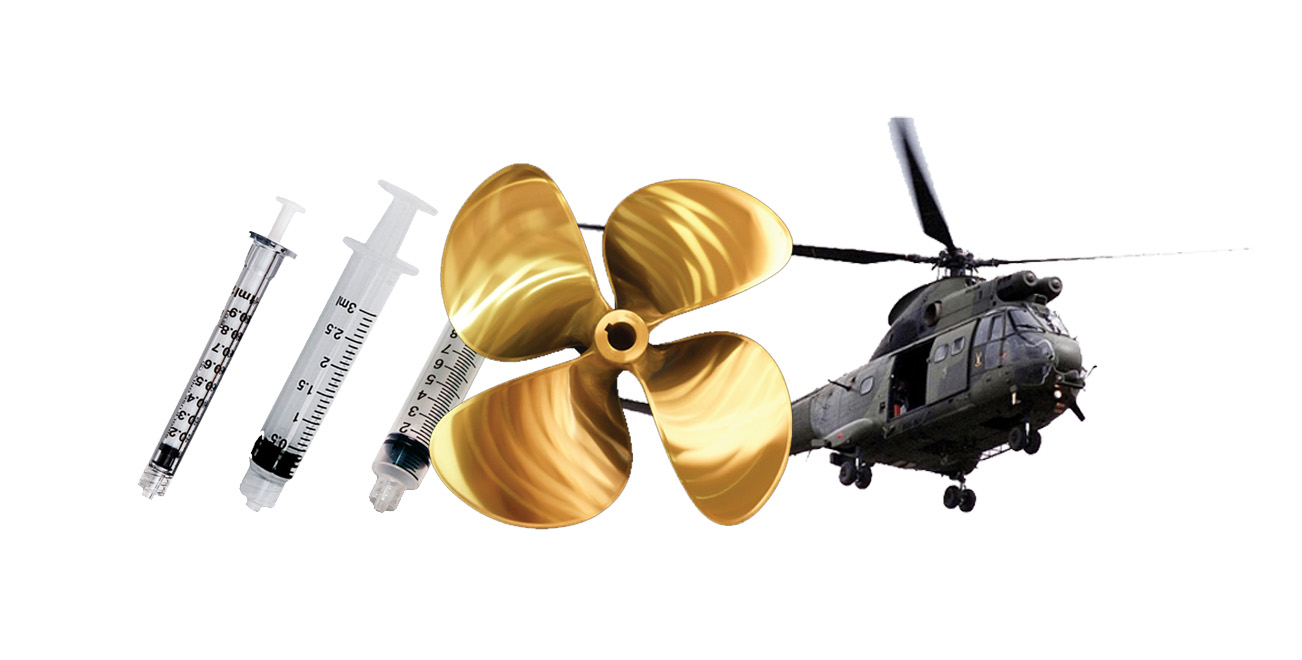
Industry Specific Reamers used in various applications for specialized reaming projects.